The fine art of tailor-made solutions
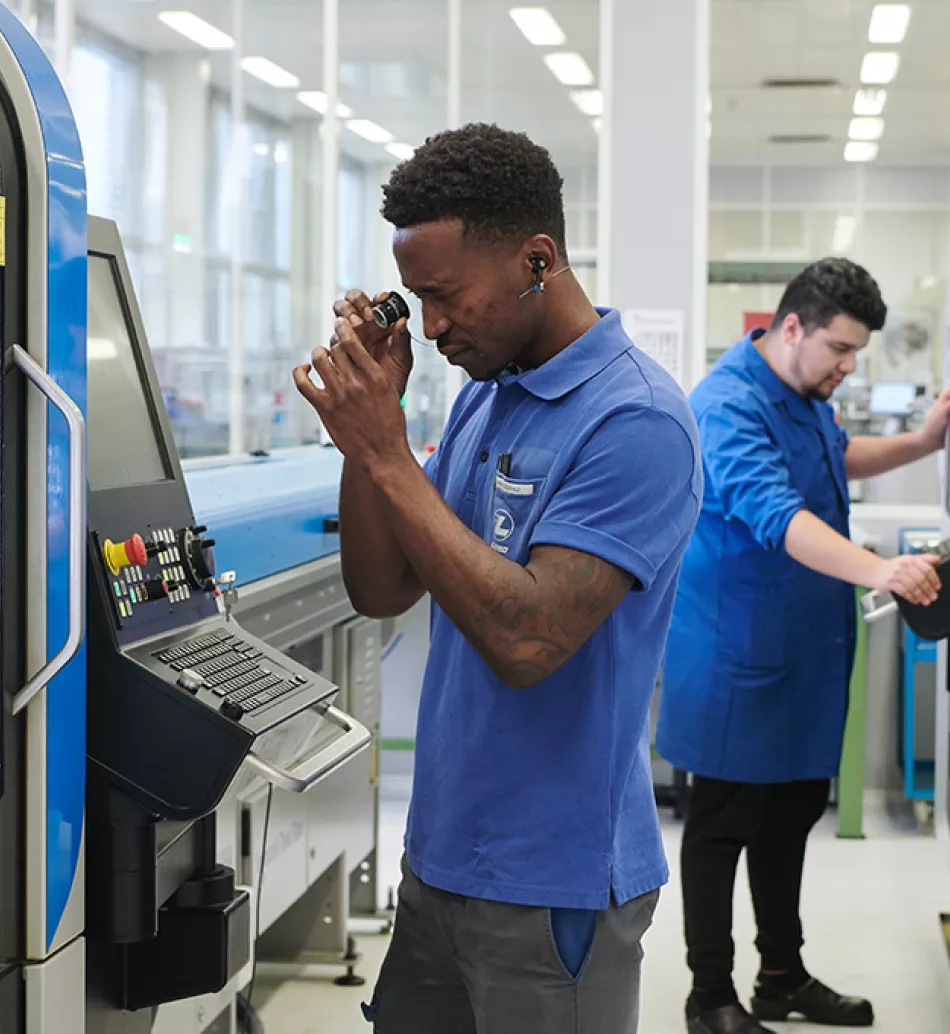
“Tailor-made” custom solutions make LEMO a special trademark.
The engineering department’s winning team ensure the company’s continued leadership in terms of innovation, performance and responsiveness.
When used in a nuclear power station, the product must not alter even after several dec- ades, in order to withstand any unexpected event. When fitted into aircraft wings, it must be ultra-lightweight and resistant to extreme temperature variations. When part of medical equipment, it must be fail-proof to guarantee every patient’s safety. The LEMO connector, irreplaceable element in a large number of demanding hi-tech applications, conveys elec- tricity, fluids and light… even several of these signals or energy simultaneously.
In order to meet its customers’ various re- quirements, LEMO offers an exceptionally vast catalogue of over 75,000 different product combinations.
What if we can still not find THE ideal solu- tion? Then LEMO invents it: every year, LEMO starts an important number of new product studies with its engineering department.
Located in the company headquarters in Ecublens (Switzerland), the department is under the responsibility of Attilio Vicario. They are at the heart of LEMO’s custom-made de- sign and innovation. Other R&D teams located at LEMO’s foreign subsidiaries: in USA, UK, Germany and Japan, complete LEMO’s special competence.
“Whenever a new study request arrives, my designers are always very enthusiastic, says Attilio Vicario. We are about to create some- thing new!”
Interestingly, the first challenge is to create the least possible number of new parts. “We only design new parts when they are really neces- sary to open up new possibilities”. This is when another quality of LEMO products becomes obvious, their extraordinary modularity. “This is how we are able to propose such a vast num- ber of different combinations, explains the engineer. This modularity makes it possible to design solutions with tried and tested compo- nents that are already perfectly under control.”
Every new request must be thoroughly reviewed by the engineering team. If the required parts are definitely not included in the catalogue, they proceed to investigate project feasibility. “In many cases, the technical specifications have to be further developed in cooperation with the customer. The deadlines are often extremely de- manding, in which case, we try and find a solu- tion, together with the customer.”
Thanks to this procedure, the number of stud- ies that are not completed has dropped con- siderably. Today over 85% of studies result in a complete order.
Careful upstream work can save a lot of time (and increase productivity). Most importantly, it guarantees a successful solution.
Once the green light has been given, the team can at last start actual development through creativity and innovative design.
Last year the department’s engineers created for example connectors conveying fluids and electric signals for a Danish company special- ized in dermatology. The team is now working on an “ultraclean” connector that doesn’t emit the tiniest particle. This project is for a com- pany manufacturing production equipment in the field of microelectronics. The requirements were extremely high. “If our connector emits a dust particle of even a few microns, the reliabil- ity of the overall equipment may be altered – tells Attilio Vicario. The smallest mistake can have important financial consequences for the customer.”
Requirements keep changing, technologies never stop evolving. The engineering depart- ment has to face ever more sophisticated challenges to propose custom solutions. How does the team know whether they managed to create something both innovative and con- form to LEMO’s standards? “Simply when they see the new product appear in the catalogue!” answers the manager.
Every new product is a small victory over the impossible, such as the creation of the 3K.93C model (see also article on page 28), which has become a standard in HDTV equipment. It is such a successful connector, that it can be found at the end of almost every single cable that broadcasts the images of the Olympic games, the football world cup and most other televised events where the slightest discon- nection would cause worldwide grumbling.