Backstage at the lion king
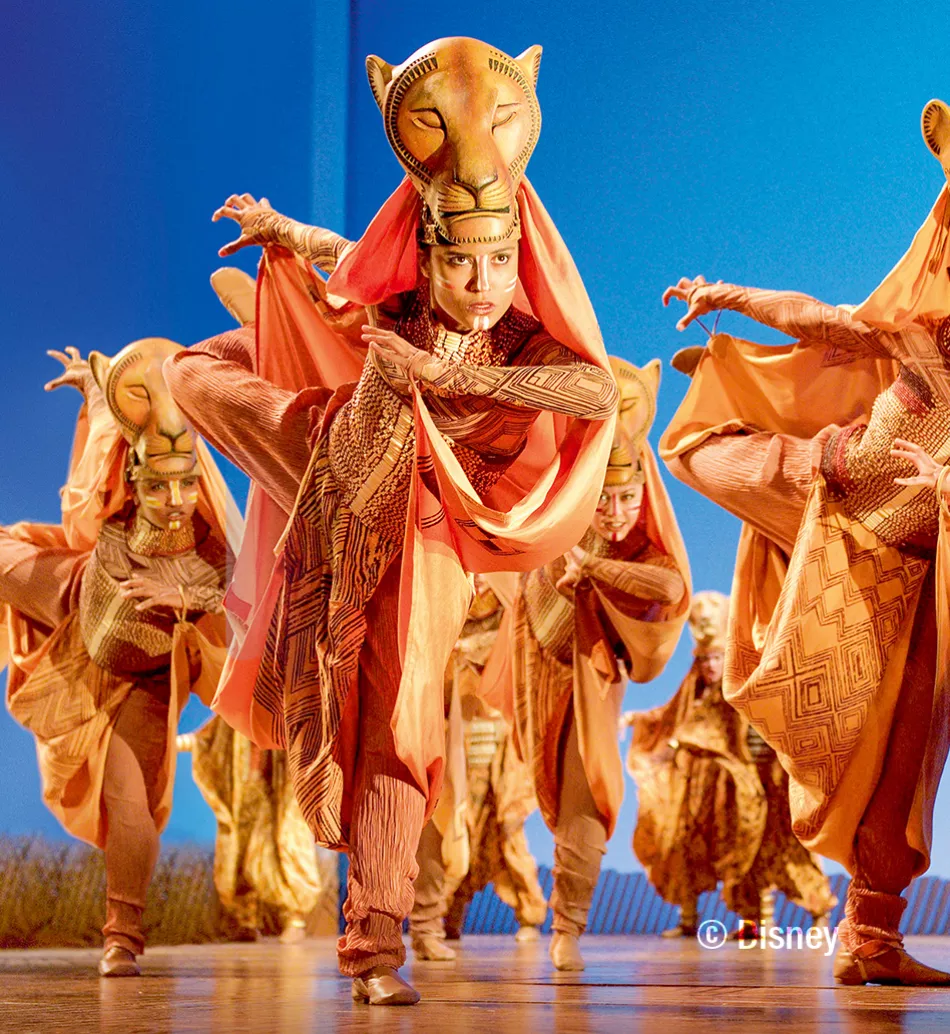
This musical blockbuster is the result of the passionate work of a great number of artists and craftspeople. Our interview with one of them, in charge of the masks and puppets of the show’s London production.
Disney’s The Lion King hit the screens in 1994. With its story of sibling rivalry, powerful images, strong personalities as well as the soundtrack composed by Elton John, the animated motion picture has seduced both young and not so young.
It raked in almost a billion dollars worldwide and became the biggest blockbuster of the year. Disney thus entered its “ second golden age ”.
Only two years later, the entertainment giant was already considering adapting The Lion King for Broadway. But how could the experience of the film be rendered on stage – the majestic beauty of the savannah, the dense jungle, the stampede of wildbeest, not to mention the cast of animal characters ?
Director Julie Taymor came up with a radical approach. Unlike the film, the musical would not stage animal characters, but humans who would represent them with masks and puppets. As for the setting, it would be reduced to a minimum, since even vegetation (grassland, exotic plants and vines) would be rendered by performers.
The scale of the production is colossal and the results have taken the audience’s breath away ever since the 1997 premiere.
There are approximately a hundred staff working backstage ; on stage, fifty or so actors, dancers and singers with elaborate costumes and make-up who act, dance and sing, bringing to life 232 puppets of all sizes, from the 15-cm mouse used as a shadow puppet, to the 4-m elephant (manipulated by four people). From giraffes (people on stilts) to flying birds (kites soaring above the audience on the end of fishing rods) and Pumbaa the warthog (an actor with a suspended costume measuring 2 m 44 and weighing 20 kg).
All in all, 25 animal species are summoned in an amazing opening sequence for “ Circle of Life. “
At the Lyceum Theatre in London, where the musical has been performed 8 times a week since 1999, the only interruption being during the pandemic, the guardian of this extraordinary menagerie of puppets is Joe Beagley. This easy-going bearded 39-yearold was still a Technical Arts and Special Effects student at Wimbledon College of Art when he started working for The Lion King back in 2005. “ I was then appointed Head of Masks and Puppets so, it’s been… gosh !.. more than 10 years that I’m heading the department ! ”
Four of his team of six (including himself) ensure the day-to-day running of the show, with the constant watchfulness of a gang of meerkats guarding its territory.
Every morning, they check everything to the finest detail. Whether the rubber tips on the crutches used by the performers are undamaged, whether the puppet mechanisms function smoothly, and the understudies are ready if required. Besides what is used in the show, there are multiples of each puppet/mask ; Zazu (the royal majordomo hornbill bird) for example, has four exact replica puppets ; one for the principal performer and three for each of the understudies. The importance of the character is reflected by the complexity of its puppet (articulated neck, beak, feet, wings, and eyelids). The understudy puppets act as a back-up and are ready to be swapped in, in case of damage mid-show. A wide variety of materials and techniques are used to fabricate these intricate masks and puppets and require a lot of maintenance. Everything must be ready before the start of the show.
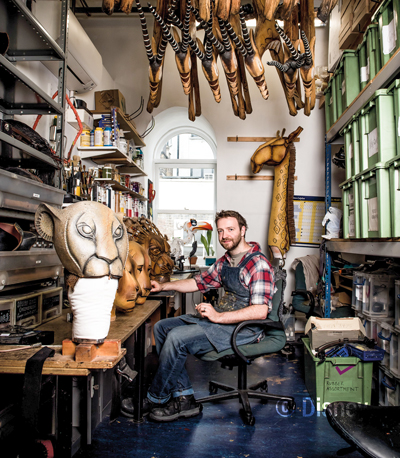
“ Safety is obviously our main concern, followed closely by the performers’ comfort ”, says Joe Beagley. “ But aesthetics are also paramount. ” Everything needs to be perfect to comply with The Lion King’s visual identity. The team closely monitors the lion masks, the originals having been crafted by Julie Taymor herself.
Two Masks and Puppets specialists touch up the paintwork regularly. Being used eight times a week, knocks and bumps are inevitable, and marks, holes and cracks are continuously repaired with carbon patches. “ It ultimately adds to the weight of the masks, so, every now and then, we do complete refurbishing as well. We do this while the performers are on holiday, so that upon their return, they find a spanking new and fresh mask or puppet ! ”
When a new mask is required, a raw carbon version is moulded by a Canadian specialist company and shipped to the local production. It is then for them to do the painting and the final touches, whilst strictly respecting the original design, to the smallest colour detail. “ The only variations accepted are a slight adaptation to the local tint of light or the skin tone of the performer ! ”
A creative associate has been touring all of the performances of The Lion King around the globe to verify their consistency, which gives an idea of the almost extreme care to detail. From the fabric feathers carefully cut for the bird puppets to the hair fitted by the hand onto the lion masks. Hence, the original masks and puppets required 37,000 hours to complete. The same attention to detail is true for all the departments – some of the 350 costumes are decorated with thousands of beads, sewn on one by one.
Why such precision ? Are these minute details really visible to spectators seated many meters from the scene ? “ It is true that we could cut corners for a number of design components. For instance, by 3D printing some of them, rather than sculpting. However, the quality of materials and of our work is visible indeed, even from a distance ! ”
Perfectionism is a core issue in terms of credibility, insists the craftsman. “ Disney is always striving for the highest quality, and the audience expects it from us. Moreover, frankly, this quest also makes us quite proud of our work ! We are part of a vast machine, but each and every one of us contributes to making the audience happy. ”
Unsurprisingly, the puppets take up most of Beagley and his team’s time. Most of the masks in the show are relatively simple and less fragile. However, two of them, the most important ones some might say, have built-in technology : those of the noble king Mufasa and his jealous brother Scar.
“ Mufasa and Scar have complex personalities and a great duality ”, explains Joe Beagley. “ To better express such complexity, Julie Taymor and co-puppet designer Michael Curry chose to use mechanically articulated masks. ”
The actors wear a discrete headgear made of thermoformed plastic, tailored to fit perfectly on their head. The articulated elbow support of the mask is fixed onto the headgear. Whenever the characters’ emotions are composed, the lion masks stay above the actors’ head, showing their facial expressions. “ But when they are overcome by their instincts, the masks are lowered and hide their faces – then their animality becomes dominant. ” This subtle trick, emphasised by the actors’ posture, results in a memorable dramatic effect.
The mechanism is controlled by the actors themselves. “ They carry a servo-box hidden in a pocket on their leg. From there, cables wind up on their back to the mask’s articulation points. Electrical cables run up their back and along their arm to a small remote control, equipped with potentiometers and switches, nestled in the palm of their hand. ” A subtle finger movement suffices to lift, lower or tilt the mask.
These hidden technologies are not subject to the same visual design restrictions as the look of the costumes. This has allowed Beagley’s team to gain directly from modernising them without compromising on the look of the show : for example, the number of cables required for articulating Mufasa and Scar’s masks have been drastically reduced. Originally, there were ten, now there are only about four.
Additionally, these cables are now no longer soldered onto the box, but rather connected by Push-Pull connectors (several LEMO B Series). “ This reduces the risks of failure and makes it possible to detect and mend the problem much faster ! ” Which is a decisive advantage, especially when a breakdown occurs in the middle of the show…
“ With 250 puppets and eight shows a week, this is inevitable ”, explains Joe Beagley. “ You just know that there will be some damage. ”
When breakdowns or malfunctions do happen, the actors just have to carry on until the end of their scene. Then, Beagley’s team will attempt to repair if possible ; replace with a spare if there is one ; or, in the worst-case scenario, patch up temporarily to keep them going until the end of the show. Once the curtain comes down, a race against the clock begins to find a solution before the next performance (sometimes the very same evening).
The most memorable incident experienced by the team involved the rather bulky elephant. The arrival of the giant puppet from behind the audience is one of the most unexpected and jaw-dropping moments of the show. However, on that day, as it was majestically walking down the aisle towards the stage, “ its skeleton kind of snapped in places ! ”
Luckily, technical problems are usually more discreet, and the audience doesn’t even realise when they happen.
According to Joe Beagley, The Lion King was the first show of such scope to use so many puppets. By the way, it is still the only one to do so on such a big scale. There must be quite a lot of pressure throughout each performance. Beagley, who also supervises the tours of the show and contributes to the adaptation of Disney’s Frozen simply shrugs. “ It is my life ; I’ve had the time to get used to it ! But it is true, that whatever may happen, the show must go on. No one, absolutely no one wants to be responsible for interrupting the show ! ”
So, obviously, when the Masks and Puppets department is recruiting, “ cool under pressure ” is among the qualities required.